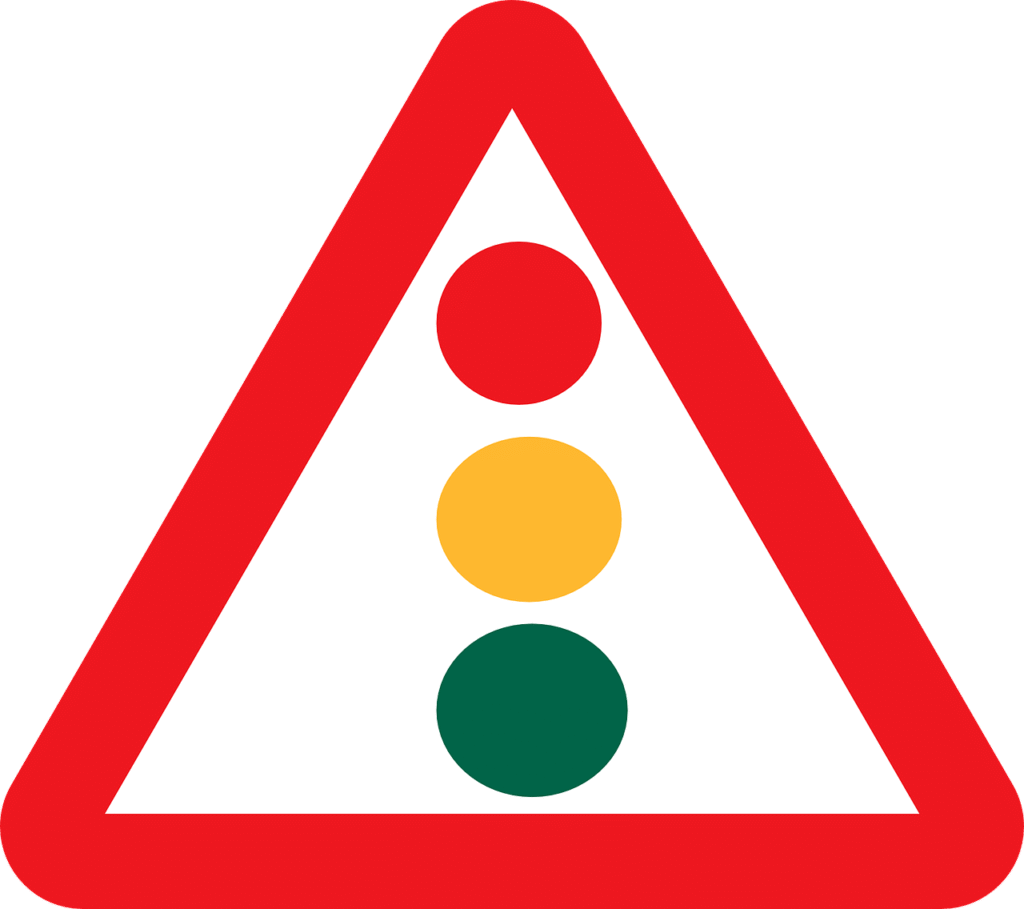
INTORDUCTION
In today’s fast-paced industrial environment, safety cannot be an afterthought. One of the most effective ways to ensure a secure working atmosphere is through a Permit to Work (PTW) system. This essential protocol not only helps in managing risks associated with hazardous tasks but also fosters a culture of accountability among team members. Understanding the intricacies of a PTW system can be the difference between a seamless operation and a potential disaster. In this comprehensive guide, we will explore the importance of implementing a robust PTW system, the key components it entails, and best practices for effective execution. Whether you’re a safety officer, project manager, or simply seeking to enhance workplace safety, this article will equip you with the knowledge to unlock the full potential of a Permit to Work system, ensuring that safety and productivity go hand in hand. Dive in, and take the first step towards a safer working environment today!
Importance of a Permit to Work System in Workplace Safety
In the dynamic landscape of industrial operations, maintaining a high standard of safety is paramount. The Permit to Work (PTW) system emerges as a cornerstone in this endeavor, serving as a critical mechanism for managing risks associated with hazardous tasks. By ensuring that all potential dangers are identified and mitigated, a PTW system safeguards both personnel and equipment, ultimately contributing to a safer and more productive work environment. This structured approach to safety management not only prevents accidents but also promotes a culture of responsibility and vigilance among employees.
The PTW system is indispensable in scenarios involving complex operations such as electrical work, confined space entry, and hot work. Each of these tasks carries inherent risks that, if not properly managed, can result in severe consequences. By mandating the issuance of permits before such work can commence, the PTW system ensures that all necessary precautions are taken. This includes conducting thorough risk assessments, implementing appropriate control measures, and ensuring that all involved personnel are adequately trained and informed.
Moreover, the PTW system fosters a collaborative approach to safety. It requires input and coordination from various stakeholders, including safety officers, supervisors, and frontline workers. This collective effort not only enhances the effectiveness of safety measures but also cultivates a sense of ownership and accountability among team members. When everyone understands their role in maintaining safety, the likelihood of incidents is significantly reduced, creating a more secure and efficient workplace.
Key Components of an Effective Permit to Work System
An effective Permit to Work system is built on several key components, each playing a crucial role in ensuring the safety of operations. The first and most fundamental component is the permit itself. This document serves as a formal authorization for specific tasks to be carried out, detailing the nature of the work, the involved personnel, and the identified hazards. It lays out the necessary precautions and control measures that must be in place before the work can begin, providing a clear roadmap for safe execution.
Another critical component is the risk assessment process. This involves a systematic evaluation of the potential hazards associated with the proposed work and the implementation of appropriate control measures. The risk assessment not only identifies the risks but also determines their severity and likelihood, allowing for the development of targeted strategies to mitigate them. This proactive approach is essential in preventing accidents and ensuring that all safety considerations are addressed before work commences.
Training and communication are also vital elements of an effective PTW system. All personnel involved in the work must be adequately trained in the specific hazards and control measures related to their tasks. Additionally, clear and consistent communication channels must be established to ensure that all relevant information is disseminated promptly and accurately. This ensures that everyone is on the same page and aware of their responsibilities, further enhancing the overall safety of the operation.
Types of Permits: Understanding Different Permit Categories
The Permit to Work system encompasses various types of permits, each tailored to address specific hazards and operational requirements. Understanding these categories is essential for implementing a comprehensive and effective PTW system. One of the most common types is the hot work permit, which is required for tasks that involve open flames, sparks, or high temperatures. This type of permit ensures that all necessary precautions, such as fire watches and the removal of flammable materials, are in place to prevent fire-related incidents.
Another critical category is the confined space entry permit. Confined spaces present unique hazards, including limited access, poor ventilation, and the potential presence of toxic gases. The confined space entry permit outlines the safety measures that must be implemented, such as atmospheric testing, the use of appropriate personal protective equipment (PPE), and the establishment of emergency rescue procedures. This ensures that personnel can safely enter and work within these challenging environments.
Electrical work permits are also a key component of the PTW system, addressing the risks associated with electrical maintenance and installations. These permits specify the isolations and lockout/tagout procedures that must be followed to prevent accidental energization of electrical circuits. They also detail the necessary precautions to protect workers from electrical shocks, arc flashes, and other related hazards. By adhering to these stringent requirements, the likelihood of electrical accidents is significantly reduced.
Steps to Implementing a Permit to Work System
Implementing a Permit to Work system involves a series of structured steps, each designed to ensure comprehensive safety management. The first step is to develop a clear and detailed PTW policy that outlines the objectives, scope, and responsibilities associated with the system. This policy serves as the foundation for all subsequent actions, providing a framework for consistent and effective implementation across the organization.
The next step is to establish a process for issuing and managing permits. This involves creating standardized permit templates that include all necessary information, such as the nature of the work, the identified hazards, and the required control measures. It also includes defining the approval process, specifying who is authorized to issue, review, and approve permits. This ensures that all permits are subject to rigorous scrutiny and that only qualified personnel are involved in the decision-making process.
Another critical step is to conduct comprehensive training for all personnel involved in the PTW system. This includes safety officers, supervisors, and frontline workers, each of whom must understand their specific roles and responsibilities. Training should cover the principles of risk assessment, the proper use of control measures, and the procedures for issuing and managing permits. By ensuring that everyone is adequately trained, the organization can foster a culture of safety and compliance.
Roles and Responsibilities in the Permit to Work Process
The success of a Permit to Work system hinges on the clear definition and understanding of roles and responsibilities among all involved parties. At the heart of the PTW process is the permit issuer, who is responsible for evaluating the proposed work, identifying potential hazards, and specifying the necessary control measures. The permit issuer must possess a thorough understanding of the work and the associated risks, as well as the authority to enforce compliance with safety requirements.
Supervisors play a crucial role in the PTW process, overseeing the implementation of control measures and ensuring that all work is carried out in accordance with the permit conditions. They are responsible for verifying that all personnel are adequately trained and equipped with the necessary PPE. Additionally, supervisors must conduct regular inspections and audits to monitor compliance and address any issues that arise during the course of the work.
Frontline workers also have a vital role to play in the PTW system. They are the ones who will be performing the actual tasks, and as such, they must have a clear understanding of the hazards and control measures associated with their work. It is their responsibility to adhere to the permit conditions and to report any deviations or unsafe conditions to their supervisors. By actively participating in the PTW process, frontline workers contribute to the overall safety and success of the operation.
Common Challenges in Permit to Work Implementation
Despite its many benefits, implementing a Permit to Work system is not without its challenges. One of the most common obstacles is resistance to change. Employees may be accustomed to existing practices and may view the PTW system as an unnecessary bureaucratic hurdle. Overcoming this resistance requires effective communication and engagement, highlighting the importance of the PTW system in enhancing safety and preventing accidents.
Another challenge is ensuring consistency and compliance across the organization. The PTW system relies on the diligent application of procedures and controls, and any lapses can compromise its effectiveness. This requires robust training programs, regular audits, and ongoing reinforcement of the importance of adherence to the PTW procedures. Establishing a culture of accountability and continuous improvement is crucial in addressing this challenge.
Additionally, managing the administrative burden associated with the PTW system can be challenging, particularly in large and complex operations. The process of issuing, reviewing, and tracking permits can be time-consuming and resource-intensive. Leveraging technology, such as digital permit management systems, can streamline these processes and improve efficiency. By automating routine tasks and providing real-time visibility into permit status, organizations can enhance the overall effectiveness of their PTW system.
Best Practices for Maintaining a Permit to Work System
Maintaining an effective Permit to Work system requires a commitment to best practices that ensure its ongoing relevance and effectiveness. One of the key best practices is to conduct regular reviews and updates of the PTW procedures. This involves evaluating the effectiveness of the system, identifying any areas for improvement, and incorporating feedback from employees. Regular reviews help to ensure that the PTW system remains aligned with evolving safety standards and organizational needs.
Another best practice is to foster a culture of safety and continuous improvement. This involves encouraging open communication and feedback from employees, promoting a proactive approach to identifying and addressing hazards, and recognizing and rewarding safe behavior. By creating an environment where safety is a shared responsibility, organizations can enhance the overall effectiveness of their PTW system.
Leveraging technology can also play a significant role in maintaining an effective PTW system. Digital permit management systems can streamline the process of issuing, tracking, and managing permits, reducing administrative burden and improving efficiency. These systems can provide real-time visibility into permit status, automate routine tasks, and facilitate data analysis to identify trends and areas for improvement. By harnessing the power of technology, organizations can enhance the overall effectiveness of their PTW system.
Case Studies: Successful Permit to Work Implementations
Examining real-world examples of successful Permit to Work implementations can provide valuable insights and lessons learned. One notable case study is that of a major oil and gas company that implemented a digital PTW system across its global operations. By standardizing permit procedures and leveraging technology to streamline the process, the company was able to significantly reduce the incidence of safety incidents. The digital system provided real-time visibility into permit status, facilitated better communication and coordination among teams, and enabled the company to track and analyze data to identify trends and areas for improvement.
Another case study involves a chemical manufacturing plant that faced challenges in managing the complexities of its PTW system. By conducting a thorough review and engaging with employees to gather feedback, the plant was able to identify key areas for improvement. The implementation of targeted training programs, the establishment of clear roles and responsibilities, and the adoption of a digital permit management system resulted in a marked improvement in compliance and safety performance. The plant was able to reduce the administrative burden associated with the PTW system and enhance overall efficiency.
A construction company provides another example of successful PTW implementation. Faced with the inherent hazards of construction work, the company developed a comprehensive PTW system that included detailed risk assessments, stringent control measures, and robust training programs. By fostering a culture of safety and accountability, the company was able to achieve a significant reduction in incidents and improve overall safety performance. The success of the PTW system was attributed to the active involvement of all stakeholders and the commitment to continuous improvement.
Conclusion and Future Trends in Permit to Work Systems
In conclusion, the Permit to Work system is an essential tool for managing risks and ensuring safety in industrial operations. By providing a structured approach to identifying and mitigating hazards, the PTW system helps to prevent accidents and promote a culture of safety and accountability. Implementing and maintaining an effective PTW system requires a commitment to best practices, continuous improvement, and leveraging technology to streamline processes and enhance efficiency.
Looking to the future, several trends are likely to shape the evolution of Permit to Work systems. The increasing adoption of digital technologies, such as mobile apps and cloud-based solutions, will continue to enhance the efficiency and effectiveness of PTW systems. These technologies can provide real-time visibility into permit status, automate routine tasks, and facilitate data analysis to identify trends and areas for improvement. The integration of artificial intelligence and machine learning could further enhance the predictive capabilities of PTW systems, enabling organizations to proactively identify and address potential hazards.
Additionally, the growing emphasis on sustainability and environmental responsibility is likely to influence the development of PTW systems. Organizations will need to consider not only the safety of personnel but also the environmental impact of their operations. This may involve the incorporation of environmental risk assessments and control measures into the PTW process. By staying abreast of these trends and continuously evolving their PTW systems, organizations can ensure that they remain at the forefront of safety management and continue to protect their most valuable assets: their people.